Tips for Trouble-Free Compressed Air
By Ron Marshall, Marshall Compressed Air Consulting
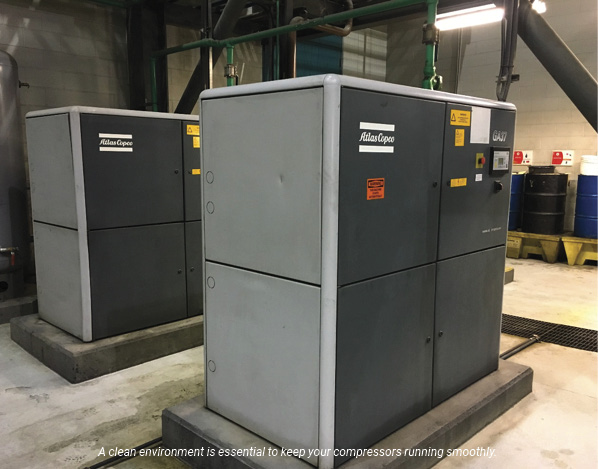
Nobody wants compressed air system problems. Low pressure, water in the compressed air, and air compressor trip outs are all unwelcome occurrences. These seem to pop up when we can least afford an outage or when production is running full blast against a tight deadline. What can we do to prevent these troubles?
Here are some tips to keep your compressed air system running smoothly:
- Understand the number one enemy of air-cooled compressors is heat. A hot environment overheats compressors and dryers making them less efficient, less reliable, and require more maintenance. Make sure your compressor room area is as cool as possible, this means making sure the heat the compressor and dryer produces is kept well away from its cooling air intake, and install a good ventilation system.
- Dust and debris in a compressor room can cause temperature problems. Realize the air compressors act like big vacuums as they tend to suck the dust and dirt from the plant environment into the compressor room, which then clogs filters, plugs up cooling surfaces, and deposits on internal compressor components. Always ensure the compressor room is kept as clean as possible. Blow down compressor after coolers regularly to ensure there is full cooling air flow. When you touch the discharge of an air compressor, it should not feel uncomfortably hot.
- Compressors squeeze water out of the ambient air when the air is compressed. Air dryers, separators and filters manage the entrained free water in a system. If the water they capture is not removed by properly functioning condensate drains, it will travel into the system piping. It is important to have a good system of efficient condensate drains and to make sure they are working through regular testing and maintenance.
- Lubrication is very important to a compressor, especially a screw type. It is even more important to maintain the compressor lubricant if the compressor is subject to overheating due to hot ambient conditions, because reduced lubricant life will occur. If your compressor cooling air temperatures are excessive, the antioxidant additives in the lubricant will break down early and allow varnish to form on the inside of cooling surfaces, ruining the heat transfer characteristics. Always maintain a good schedule of lubricant and filter changes to prevent this problem.
- Having good backup capabilities is essential. For maximum reliability, you should have enough spare compressor and air dryer capacity to be able to withstand the failure of your biggest compressor and still be able to maintain adequate system pressure. To ensure you have enough capacity, you should have regular compressed air system audits to measure your peak production demand and system efficiency.
- Air compressors are like automobiles, you should not expect them to last forever, especially if they are running on a 24-hour, seven-day-a-week schedule. When maintenance problems start occurring on a regular basis, it may be time to renew. The next purchase may be an opportunity to buy a more efficient compressor, and if so, your next purchase may be partly covered by local power utility incentives.