Retract Coil Burn-Out
Workers at a private contractor that makes torpedoes for the U.S. Navy were having a problem with an assembly line directional valve coil that would burn out often, causing production issues. The valve, a D05, three-position, spring-centered, 115-volt AC explosion-proof design, continually lost the retract side “air gap” solenoid coil. The assembly line took six months to install and debug. Once it was turned over to production, this problem started showing up.
The OEM sent a new valve, thinking there must be a problem with the original unit. It didn’t help. The contractors’ electrical engineer suggested they interchange the “A” and “B” ports to the cylinder and do the same with the two coils. The problem still persisted. Whichever coil controlled the retract function would eventually fail. The pump delivered 20 gpm, and the valve was rated for 26 gpm.
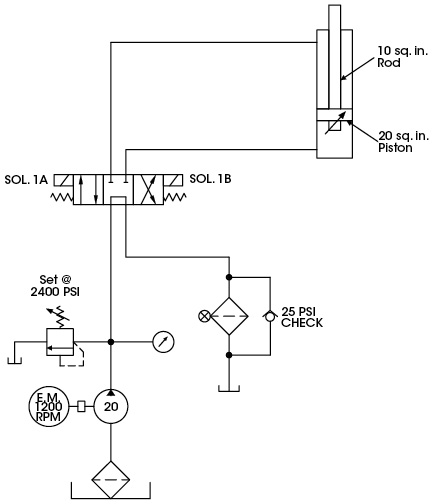
Any idea what was causing the problem?
See the Solution
The D05 explosion-proof valve that was used on the Navy torpedo line had an air gap designed coil. This style of coil needs to fully shift for the high in-rush amps to drop to the low holding amps. This shouldn’t have been a problem, especially for new valves. However, because the cylinder has a rod to cap end area ratio of 2:1, the returning oil from the retracting cylinder would force 40+ gpm flow through the directional valve that’s only rated for 26 gpm. Many valve spools will try to move to the center position when their maximum flow rate is exceeded. This will cause the air gap solenoid to move off of the fully shifted position, increasing the holding amps causing the coil to fail. The OEM replaced the D05 valve with a larger valve to solve the problem.
By Robert Sheaf, CFPAI/AJPP, CFPE, CFPS, CFPECS, CFPMT, CFPMIP, CFPMMH, CFPMIH, CFPMM CFC Industrial Training
The reason for the solenoid burning out is due to the fact that when 20gpm (from the pump) is pushed into the rod end during retraction, 40 gpm is pushed out of the cap end and back through the directional valve due to the differential areas of the piston. This is higher than the rated flow of the valve.
This would likely cause the valve spool to try to offset the solenoid enough that it would cause it to overheat and fail.
I agree with Jesse’s comments…the higher flow rate that would be experienced from the cap end of the cylinder during retraction is to blame for the coil failure.
The force created on the spool from the oil exiting the cap end exceeding the valves rated flow would be working directly against the force created by energizing the retract solenoid.
You can find reference to this in many valve mfg’s technical data and is commonly referred to as ‘malfunction flow’. Basically what that means is the force created by flow paths in the spool exceed the solenoid coils ability to hold the spool in position.
It can also vary from depending on the spool function. Read the charts and literature carefully.
For this problem a valve rated >40 GPM would be the answer or reduce the available flow from the pump to <13 GPM.
Low voltage or a bad ground for the retract solenoid would require higher amperage through the coil. Higher amperage means higher temperatures, Switching the coils AND the hoses did not change the power supply to the retract coil. Simple tests with a multimeter will identify the root cause.
I agree with Jesse. The flow forces created by the excessive flow caused the spool to oppose the direct acting solenoid to the point where it overheats and eventually fails.
The OEM should account for the adjusted flow exiting the larger area of the cylinder. The adjusted flow is more than the 26 gpm flow rating of DO5 valve. The coil is consuming more power to offset the increased flow forces through the spool valve. The coil has reached its power limit and will continue to fail. The OEM should switch to larger spool valve like DO7 to handle adjusted flow during retraction.
The retract. Coil was being energized before the extend coil fully dissipated its electrical field. The solution is to put a time delay in the PLC. This can happen with AC coils
In this case the return flow rate is 40 GPM and the directional control valve always overheated because of throttling causing coil fail the solution suggested is to replace the valve size to allow return flow rate passes through it without overheat
the theoretical velocity of the cylinder when retracting is 7.68 inches per second.
The volume of oil in the blind end of the cylinder when exhausting back through the directional valve at this velocity is 39.6 g.p.m. which exceeds the valve’s rated flow by more than 50%.
The forces on the valve spool with this flow rate likely try to force the spool back against the solenoid resulting in an over-amp situation and overheating the coil. every time the cylinder retracts.