Gold Mine Crusher with Erratic Pressure
A hydraulic power unit operating a rock-crushing machine had erratic pressure problems, causing the crusher to stall when the pressure seemed to relieve at a lower pressure than needed. The machine was over 30 years old and was somewhat quite simple in design.
The circuit attached shows the main relief valve remotely controlled so the operator could reverse the motor’s rotation with the directional valve and adjust the pressure higher than normal to clear jambs. Once the jamb was cleared, he would reset the pressure back to the normal setting and shift the directional valve back to rotate the crusher motor in the normal operational direction.
They determined that the remote control relief valve was worn badly and needed to be replaced. Their storeroom had the same brand of relief with the same spring range, but with just one letter difference in the model number. They installed it in the manifold, adjusted the valve from fully open to the number of turns closed used by the old, similar valve with the same spring rating, and then started the system up. It seemed to run fine until the crusher jammed and blew the side of the pump out. Luckily, no one got hurt.
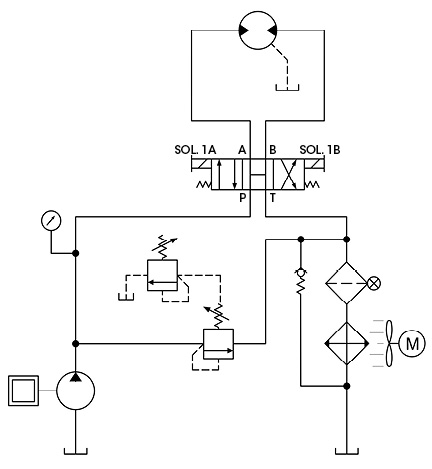
What could have caused the problem?
See the Solution
The gold mine power unit where the side of the pump blew out had a relief valve installed that had the inlet and outlet reversed, taking the pilot relief out of the circuit. Without a drain, the main relief would not open, causing an unwanted pressure spike that blew the side out of the pump. Sun, Parker, and Eaton all over the years have produced relief valves where the pressure inlet comes into the side and out the bottoms, as well as units that have the inlet in the bottom and out the side.
It’s so important to verify which ports on the manifold or housing are inlet and outlet, and that the screw-in cartridge matches the same configuration.
By Robert Sheaf, CFPAI/AJPP, CFPE, CFPS, CFPECS, CFPMT, CFPMIP, CFPMMH, CFPMIH, CFPMM CFC Industrial Training
Hi Bob,
Mistake number one, they should have checked to see what the difference in model code meant.
It is possible that the replacement valve was installed backwards, or in the case of a cartridge type valve the porting was reversed. In either case there was no relief protection so pressure reached an unsafe level until something failed.
Regards,
Bert
Good morning, Bob. The model code difference likely indicated an external drain configuration on the new relief valve. The blocked spring chamber thus prevented the valve from relieving and, when the crusher jammed, system pressure rose until mechanical failure occurred. Lesson Learned – ALWAYS test and verify operation of a pressure control device BEFORE mounting it into your customer’s very expensive hydraulic system. (One comment worth noting re. springs in relief valves …. It is standard practice to convert one pressure range to another by switching springs and shims. This is okay as long as the final assembly is tested to verify maximum relief pressure setting is achieved without the spring going solid; the different spring range likely has a different solid length and will certainly have a different spring rate requiring shims to trim it into tolerance. It is again worth noting that every time a valve is modified, or even reassembled with the same parts, performance testing is required.) -Richard McAfee, Texas Hydraulics, Inc.
I have to agree w Mr. McAfee. The valve looks just like a Vickers/Eaton C_5 however the model code indicated it was configured as a sequence vlv requiring an external drain. Without the drain the valve will likely exceed the intended pressure. BOOM!
Hello,
I just reviewed the mine crusher problem explanation and schematic, and with the information given, I’ve come up with two possible errors.
1. The difference of the one letter in the model number could’ve meant the difference between an externally or internally drained valve, or externally or internally piloted valve. I think either one of these mismatched porting conditions for the remote relief could have caused a critical pressure build-up to develop. I whole-heartedly concur with double checking a replacement valve’s design configuration before installing it to make sure it matches the old one.
2. The explanation said, “the machine was 30 years old” and they found the remote relief to be “badly worn”. Using the information given that they used the method of counting turns on the old relief and set the new relief accordingly and then just started-up and ran the system, it seems very possible that the spring setting of a 30 year old remote relief – that had been reset constantly over it’s lifetime – had a much different setting because of its weakened spring than a new relief with the same spring rating, and, if “badly worn” meant that the the needle and seat of the old relief were eroded, well then, with a new, strong spring and tight seal at the needle and seat, the same number of turns would result in a much higher relief setting. I’ve learned a good rule of thumb to be; If I’m installing a relief on any system and doing a start-up procedure, I restart the system with the relief back out and use reliable gauges installed in the system, at the appropriate places, to test the new relief and run it up to the recommended setting. I didn’t see anything mentioned about a restart procedure.
Just my thoughts with the info given.
Sincerely,
Robert Wenck, Jr.
Hydraulic Specialist
Hydraulic Works Inc.
Thank you for writing about Gold Mine Crusher and its Erratic Pressure problem. I think we can avoid problem like this if we keep a regular maintenance routine.