Hydraulic Hose Assembly Application Guidelines – ISO/TS 17165-2
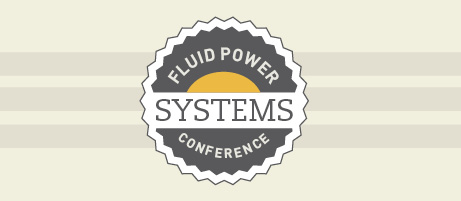
Hydraulic hose and hose assemblies require careful selection, fabrication, installation, and maintenance to reduce the likelihood of component or system failure, thereby reducing the risk of personal injury or property damage. This article is a review of the application guidelines for hydraulic hose and hose assemblies listed in ISO/TS 17165-2, which was updated and published in April 2013.
Hydraulic hoses, due to their pressure, temperature, and proximity to the operator, can cause severe personal injury and property damage. Some of the recommendations in ISO/TS 17165-2 can also apply to other hoses, such as industrial and automotive hoses.
This part of ISO 17165 provides guidelines for selection, routing, fabrication, installation, replacement, maintenance, and storage of hose and hose assemblies for hydraulic fluid power systems, which are manufactured from hoses conforming to ISO 1436, ISO 3862, ISO 3949, ISO 4079, and ISO 11237, and hose fittings conforming to the six parts of ISO 12151.
The main reason for this technical specification is to promote safety when using hydraulic hose assemblies.
The list of potential conditions and situations that can lead to personal injury or property damage described in ISO/TS-17165-2 is not necessarily all-inclusive. Reasonable and feasible means shall be taken into consideration to reduce the risk of personal injury, property damage, or both. Training, including the information in ISO/TS 17165-2, for operators, maintenance personnel, and other individuals working with hose assemblies under pressure is encouraged.
Below are some of the most common injuries with hydraulic hose:
- Fluid injections: Fine streams of escaping pressurized fluid can penetrate skin and enter a human body. These fluid injections can cause severe tissue damage and loss of limb.
- Whipping hoses: If a pressurized hose assembly blows apart, the hose fittings can be thrown off at high speed, and the loose hose can flail or whip with great force.
- Burns from conveyed fluids: Fluid power media (that is, hydraulic fluid) can reach temperatures that can burn human skin.
- Fire and explosions from conveyed fluids: Most fluid power media, including fire-resistant hydraulic fluids such as phosphate esters and polyol esters, can burn under certain conditions. Fluids that escape from pressurized systems can form a mist or fine spray that can flash or explode upon contact with an ignition source.
- Fire and explosions from static-electric discharge from fluids: Fluid passing through hose can generate static electricity, resulting in static electric discharge. This can create sparks, which can ignite fluids in the systems or gases in the surrounding atmosphere.
- Electrical shock: Electrocution could occur if hose conducts electricity through a person. Most hoses are conductive. Many contain metal or have metal hose fittings attached. Even nonconductive hoses can be conduits for electricity if they carry conductive fluids. This should be kept in mind when routing or using hose near electrical sources.
- Mechanisms controlled by fluid power: Mechanisms controlled by fluid power can become hazardous when a hose fails.
Each system should be carefully analyzed.
Routings should then be designed, and hose and related components should be selected to meet the system performance and hose service life requirements, as well as to minimize the risks of personal injury, property damage, or both. The following factors should be considered:
- System pressures (internal and external)
- Suction
- Temperature
- Permeation
- Compatibility between hose materials and system fluids
- Environment
- Static-electric discharge
- Sizing
- Unintended uses
- Specifications and standards
- Unusual applications
- Hose assembly cleanliness
- Hose fittings
- Vibration
- Hose cover protection
- External physical abuse
- Swivel hose fittings and connectors
- Rotary connectors
- Slings and clamps
- Minimum bend radius
- Elbows and connectors
- Lengths
- Motion absorption
- Tolerances and machine motion
- Change in hose length due to changes in pressure
- Hose movement and bending
Persons fabricating hose assemblies should be trained in the proper use of equipment and materials.
The manufacturers’ instructions and the practices listed in ISO/TS 17165-2 should be followed. Properly assembled hose fittings are vital to the integrity of a hose assembly. Improperly assembled hose fittings can separate from the hose and can cause serious injury or property damage from whipping hose or from fire or explosion of vapor expelled from the hose. The following steps should be taken when fabricating hose assemblies:
- Component inspection: Prior to assembly, components should be inspected for style, type, cleanliness, loose covers, corrosion, nicks, dents, scores, burrs, sharp edges, size, inside obstructions, visible defects, damage, length, and blisters.
- Hose fitting parts: If hose fitting parts from different manufacturers are used in the same hose assembly, the performance of the hose assembly should be verified by testing in accordance with ISO 6605.
- Compatibility between hose and hose fittings: Hose from one manufacturer is not usually compatible with hose fittings from another, and they should not be intermixed without approval from both manufacturers.
- Hose assembly equipment: Equipment for fabricating hose assemblies from one manufacturer is usually not interchangeable with that from another manufacturer. Hose and hose fittings from one manufacturer should not be assembled with the hose assembly equipment of another manufacturer, unless approved by the hose-fitting manufacturer.
- Safety equipment: During fabrication, proper safety equipment, including eye protection, respiratory protection, and adequate ventilation should be used.
- Condition of hose assembly parts: Hose assemblies should be made from hose that is undamaged and unused, and hose fittings that are undamaged and either unused or intended to be reused.
- Cleanliness of hoses and hose assemblies: Hose assemblies can be contaminated during fabrication. Hoses and hose assemblies should be cleaned to specified cleanliness levels.
- Temperature: The fabrication of hose assemblies should be performed at an ambient temperature over 0°C or 32°F, unless otherwise recommended by the manufacturer.
- Assembly Inspection: After assembly, examine hose assembly for visible defects and interior obstructions, such as tube bulges, etc.
- Marking: Hose assemblies shall be marked in accordance with ISO 17165-1. Marking shall remain permanent and legible.
The following practices should be used when installing hose assemblies in new systems or replacing hose assemblies in existing systems.
The manufacturer should make available additional instructions on mounting, storage, and operating conditions.
- Do a pre-installation inspection.
- Handle the hose assembly with care during installation.
- Secure and protect the hose assembly from external damage.
- Route the hose away from any obstructions.
- Do not twist the hose.
- Follow the recommended assembly torques.
- Do a system checkout.
A hose and hose-fitting maintenance program can reduce equipment downtime, maintain peak operating performance, and reduce the risk of personal injury, property damage, or both.
The user should design and implement a maintenance program that suits the specific application and each specific hose in that application, and the maintenance program should include the following:
- Inspection frequency
- Visual inspection of hose and hose fittings
- Visual inspection of all other components in the system
- Functional tests
A system of age control should be maintained to ensure that hose is used before its shelf life has expired.
Shelf life is the period of time when it is reasonable to expect the hose to retain full capabilities for rendering the intended service. Hose should be stored in a manner that facilitates age control and first-in, first-out usage based on the manufacturing date on the hose or hose assembly. Unless otherwise specified by the manufacturer:
- The shelf life of rubber hose in bulk form or hose made from two or more materials is 28 quarters or seven years from the date of manufacture, with an extension of 12 quarters or three years, if stored in accordance with ISO 2230.
- The shelf life of thermoplastic and polytetrafluoroethylene hose is considered to be unlimited.
- Hose assemblies that pass visual inspection and proof test should not be stored for longer than two years.
Hose and hose assemblies should be stored in accordance with the storage conditions defined in ISO 8331.
When storing hose, care should be taken to avoid damage that could reduce hose life. The manufacturers’ information for storage and shelf life should be followed. Examples of factors that can adversely affect hose and hose assemblies in storage are
- temperature and humidity;
- ozone, ultraviolet light, direct sun, or heat rays;
- oils, petrol or gasoline, kerosene, or their vapors and solvents;
- corrosive liquids and fumes;
- rodents and insects;
- radioactive materials;
- sharp edges and abrasive surfaces; and
- electric or strong magnetic fields.
For more information: This article is based on a presentation at the 2013 Fluid Power Systems Conference held in Rosemont, Ill., from November 19-21, 2013. Contact Luis Moreiras at
LMATHTS@aol.com.
Plan to attend the next Fluid Power Systems Conference in Spring 2015.
You said that temperature and humidity affect hydraulic hoses. Maybe I should ask a professional for assistance when I am looking for somewhere to store them. It could also be helpful to find a professional is able to teach you about different ways to care for the hydraulic hoses.