Overheating on a Large Forging Press
A forging and stamping company had problems with overheating on a press. The company had several identical presses, and only one had been overheating for some time. The employees added a larger heat exchanger a few months back, but they recognized that this was not the correct solution since the other identical presses worked well.
The circuit shown in Fig. 1 has been simplified; the unit had three pumps working together, several cylinders connected in parallel, and several accumulators all tied together. All the machines had identical kidney loop cooler and filtrations systems that were proven to be working properly.
The only feedback we could get on the overheating machine was the loud banging noise when the machine was shut down. This was caused by the accumulator circuit discharge rate not being throttled down properly. But this shouldn’t have caused an overheating problem. The employees found that one pump’s compensator was set slightly higher than the safety relief. When its pressure was set properly, the overheating problem lowered a few degrees, but that wasn’t causing the main overheating problem.
The overheated oil was coming from the main manifold. They screwed the flow control rod on the 16-mm cartridge all the way in to lock the moving element in place, thinking it was popping open each cycle. It didn’t solve the problem. The main safety relief was set properly.
Click on image to enlarge.
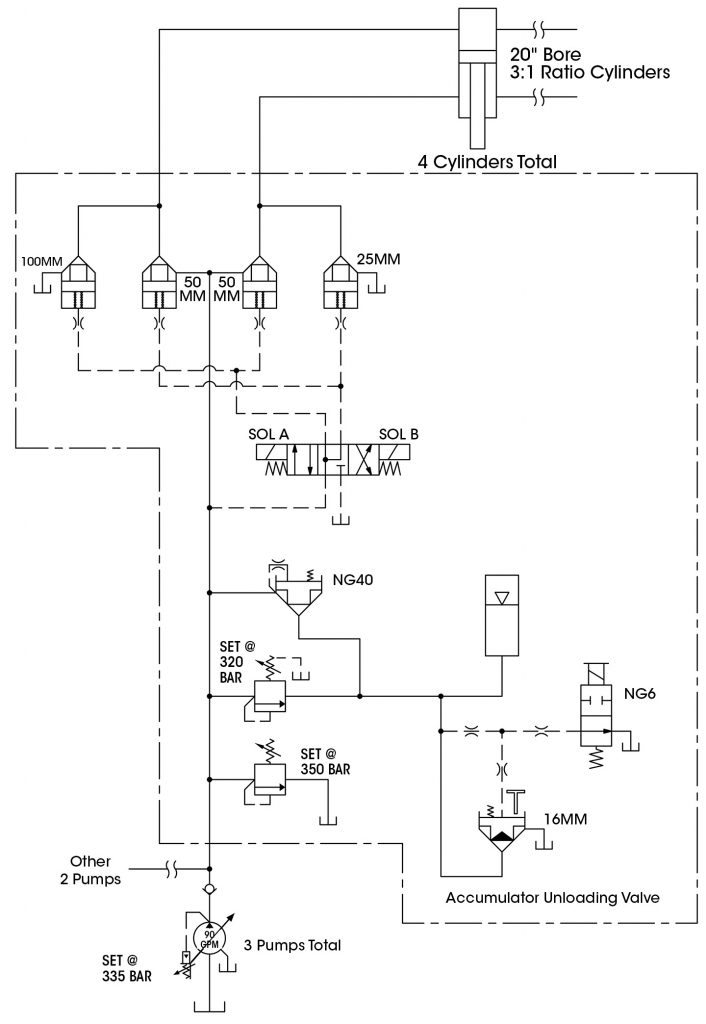
Any idea what could be causing the problem?
See the Solution
When the workers couldn’t find a problem causing overheating on the press, they started removing each component one by one hoping to find something that failed. When they got to the accumulator unloading valve, they found the sleeve and moving poppet were eroded away, allowing 335-bar fluid to discharge to the tank. This would heat the volume of oil leaking back to the tank up approximately 30 to 35°F. They pulled the sleeve out of the manifold and also found that the steel surface around the “B” side of the sleeve was badly eroded as well, but not to the point it would cause a problem.
High-velocity 335-bar oil discharging to a low-pressure tank line can cause cavitation. The fix was to add a 5-bar check valve to the tank line after the logic valve where it leaves the manifold. This back pressure is enough to prevent the cavitation bubbles from forming and eliminating the erosion problem.
By Robert Sheaf, CFPAI/AJPP, CFPE, CFPS, CFPECS, CFPMT, CFPMIP, CFPMMH, CFPMIH, CFPMM CFC Industrial Training
Heat is a direct byproduct of leakage and making the assumption that the poppet valves are in working order having passed manufacturing quality control. The second factor in my conclusion is based on the other three machines operating correctly. The only variable in the system that could produce this much heat would be a flaw in the manufacturing of the manifold itself. My conclusion is one of the poppet cavities has been machined to deep. I would start by looking at the cavity dimensions in the manifold. I would start at the 16mm cavity then move to the 40mm and then the 50mm. A second possibility is break through between cavities.
Thank you
George Lutz CFPPS
The first thing I would check is to verify NG6 is energizing when it should.
First thing I would check is that the 25mm valve is plumbed to the rod side of the cylinders and the 100mm valve is plumbed to the cap end of the cylinders as the drawing shows. If the 25mm valve is plumbed to the cap end of the cylinders the intensified flow over this valve could be causing the heat.
I would use a thermometer on the components to see where I was generating the excess heat. you have (3) working systems to compare to. in this case, the faulty valve would show up quickly as the potential source of the heat generation.
The fact that fluid has to go over a 320Bar relief valve to fill the accumulators is creating heat.
If the accumulator unloading valve is leaking, then fluid will constantly be going over a 320bar relief. This is where you are generating heat. Fix the leak in the unloading valve.